Continuous production of engineered flooring
CSP production line for parquet flooring
Opportunities
- Parquet flooring without a break in the core material
- Parquet flooring with assembled core material
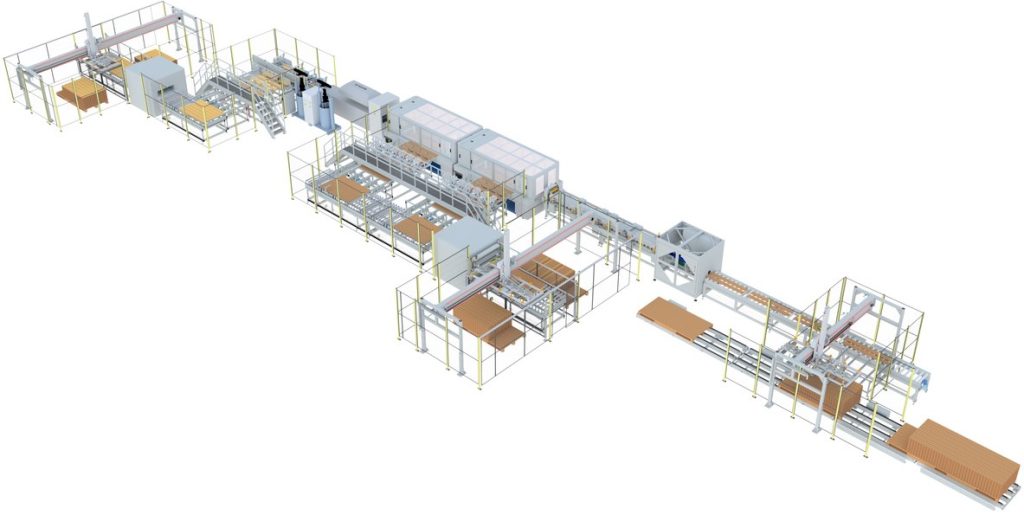
The destacker removes the core material from the pallet and places it in the production line. There are two safety zones with one pallet each. When one pallet is empty, the destacker continues with the other pallet.
The sander calibrates the thickness and surface of the core material.
According to the product one wants to make, glue is applied to the end face of the wood and over the full width of the boards. Thus, the wood is glued into an infinite strip of wood. This function can also be switched off if one does not want interruptions in the core material.
The glue is in two barrels. When one barrel is empty, it also automatically switches to the other barrel.
The subfloor is heated with infrared emitters before thermoplastic hot melt adhesive is applied over the entire surface of the core material.
Now the subfloor arrives in the assembly units. The windows in these units provide a clear view of the process. An internal camera system verifies each board before the assembly unit applies the top layer to the subfloor.
This is because the top layer of the parquet is simultaneously removed from the pallet by a second destacker.
This top layer is sanded and presented to the assembly units.
In the assembly units, the top coats are applied to the bottom coats.
The glued layers then pass through a segmented press.
And then through the flying saw that cuts precisely between the top layers, as they determine the length of the parquet floor.
Finally, the automatic stacker goes back to making nice packages from the parquet.
Large and small systems
We build systems for every user. Are you looking for a small or a large production line?
That's no problem at all, we are happy to help you with this.
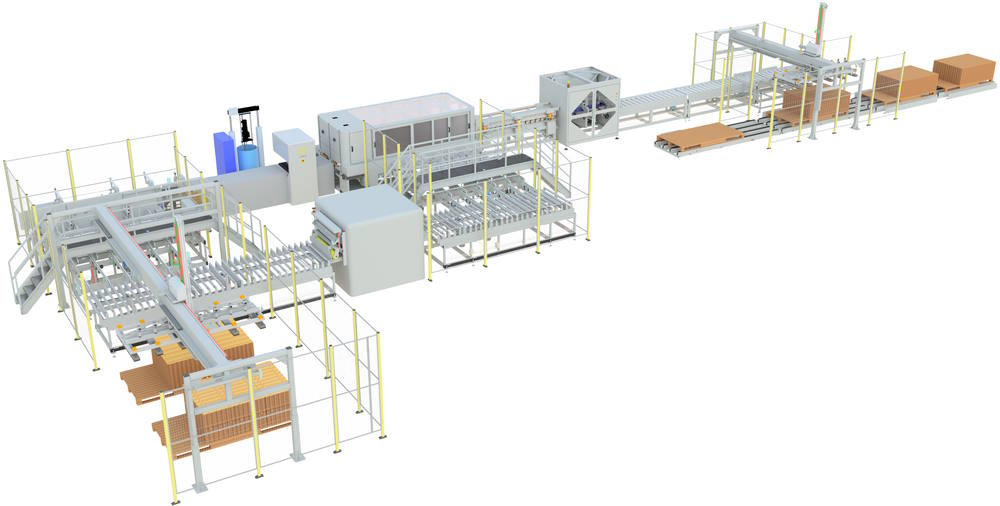
The power of this production line is impressive, because did you know:
- all conversions are automatic (the line automatically switches to other formats)
- even small batches or quantities are easily produced with a theoretical minimum of a single piece
- the line can work on its own with one supervisor
- instead of using an infinite strip of wood, it is also possible to opt for 1-to-1 assembly of subfloor and top layer, when they have the same dimensions.
Get in touch
The PAR-Colle production line is a modular concept that can be adapted to your specific needs and wishes.
We are happy to discuss the possibilities with you in order to realize the most suitable solution for your company.
Call us!
+32 14 37 77 52